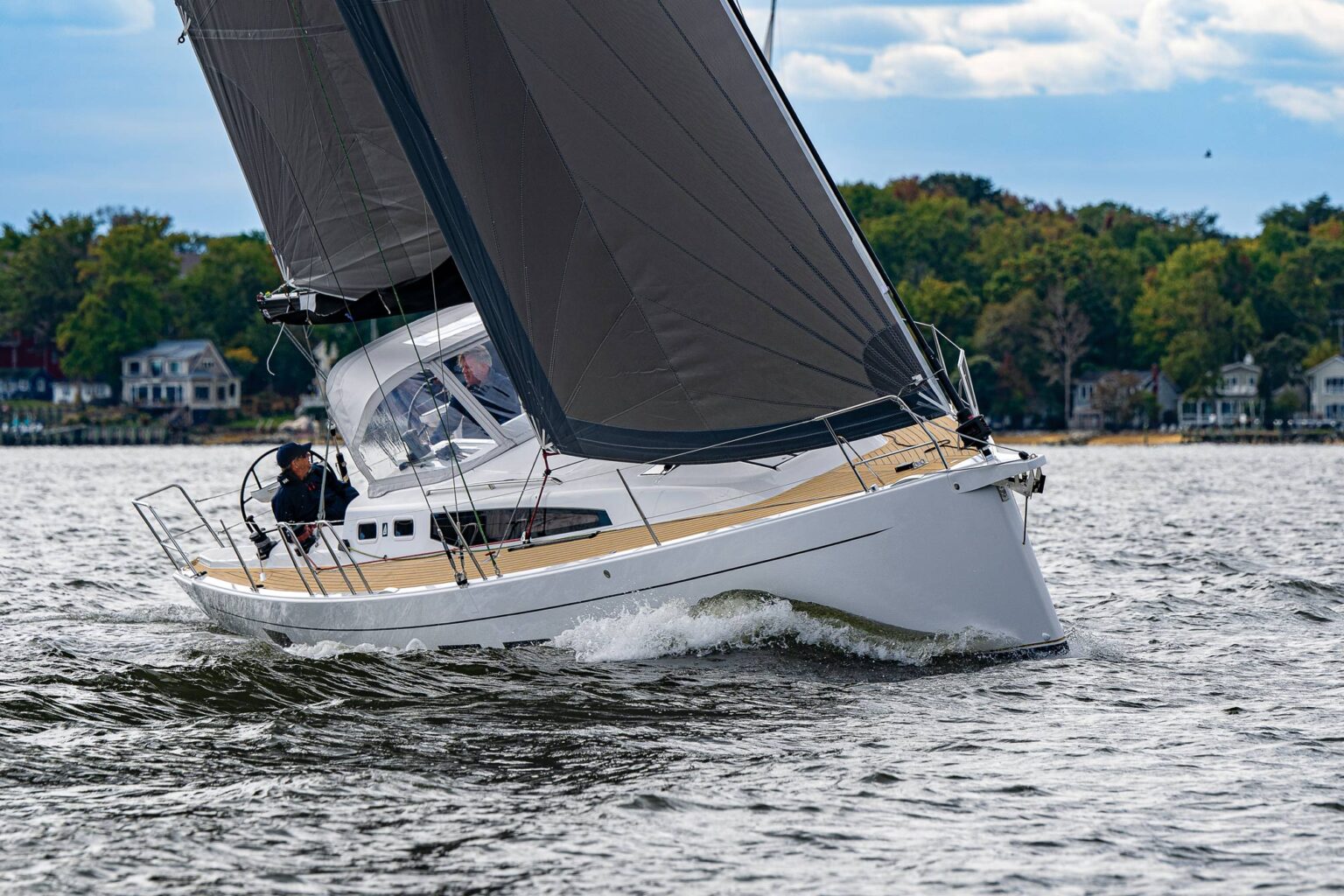
J/40 Reborn: A Legendary Cruiser Reinvented for a New Generation
Like father, like son. Al Johnstone’s modern J/40 follows in the award-winning wake of the original—and wins big in 2025.
Like father, like son. Al Johnstone’s modern J/40 follows in the award-winning wake of the original—and wins big in 2025.
A quest for cruising perfection turns into a battle with fickle winds, strong tides, and blistered hands in the Salish Sea.
In the hypercompetitive world of offshore solo yacht racing, Ambre Hasson is charting her own ambitious course.
The Neel 52 redefines what’s possible in multihull cruising, blending volume, comfort, and offshore-ready performance.
Top boatbuilders from around the globe are set to compete for the prestigious Boat of the Year award at the Annapolis Sailboat Show.