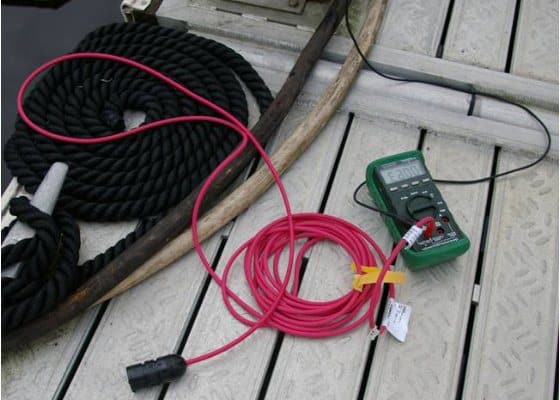
corrosion test kit_001_8324.jpg

Typical hull potential test set-up
We received an interesting comment regarding our earlier post, “To Bond or not to Bond”. It’s worth sharing so that people will understand some of the dynamics involved with that case. So, here is the comment:
Ed- “The comment I have on this situation is that given the original installation was done poorly, what is to guarantee the addition of a bonding cable would have been done any better? Regardless of how it was installed (bonding or no bonding), for my money, I would have expect that testing with a silver/silver – chloride cell being thrown over the side was done to make sure there was nothing amiss. A relatively simple and relatively cheap task given the risks.
In a similiar situation and a previous life, I demanded that a megohm test be done on all cabling pulled through metal conduit to make sure that the insulation on the cabling was still intact. I was burned once and doing this testing afterwards never let me down again.
To my knowledge, there is no type of QA checks like this in the ABYC standards. Should something like this be considered or have I missed it?”
Thanks,
Ken
So, let’s walk through this step-by-step. First of all, many of you may not be familiar with what Ken is referring to when he mentions the silver chloride cell. In the photo above the black cylinder at the end of the long red cord plugged into the multi-meter is a silver chloride reference cell. Many corrosion analysts use these cells to provide a constant and reliable sensor for detecting low level milli-volt readings with the meter. The cell is put into the water the boat being checked is sitting in and plugged into the “com” lead socket on the meter. The + lead on the meter is connected to the boat’s grounding system. The meter gets turned to the DC volts scale and a reading of hull potential is measured. This potential reading is an indicator of whether or not the boat is equipped with enough anodes to protect the underwater metal on the boat. It’s important to note that the acceptable readings will vary depending upon what the anode material is made of, either zinc, aluminum alloy or magnesium alloy, and what the salinity level of the water the boat is floating in. Keep in mind here that this is all a measurement of galvanic level voltage potentials. Typically 1.6 VDC or less. Now in the case we are discussing here, there was a situation where battery level voltage potential was leaking out through the light fixture. So, would that have shown up if the boat had been checked prior to the boat being delivered to the customer? Yes it might have as long as the light was activated at the time of the test. But to Ken’s point that this should be a routine test that a boat builder performs as part of a general quality assurance test, that may not be practical in the real world. Let me explain why.
The actual hull potential reading for a boat is going to vary depending on a variety of environmental factors including water salinity, temperature and water flow (tidal currents). So, to be accurate, these tests need to be made in the location where the boat is going to be spending most of it’s time in the water. In most cases, the boat builder has absolutely no idea where the boat is going to end up living, so precise levels of cathodic protection (what we are talking about here) are difficult to achieve at the factory. So in my view, cathodic protection levels really should be part of a delivery inspection once the boat arrives at its home port. I don’t know of any builder that actually does this. Most builders install a few anodes on the boat in the usual places and hope for the best.
As for Ken’s thinking that questions whether or not bonding the subject boat would have made any difference in the first place, I can say definatively that had the boat been bonded in this case, the boat would have been saved.
As to whether the ABYC has QA test requirements within it’s standards at all, yes we do. ABYC standard H-24 for example, requires a boat builder to pressure test every gasoline fuel system as installed to ensure that no leakage is present.
You see, the ABYC standards are generally classified as safety standards. So, this begs the question about what constitutes proper levels of safety. Ken is quite right that we require no such broad based safety checks for electrical systems as installed. In this case, the fellow that bought the boat which sank was intending to do a lot of offshore sport fishing. If the light fixture had failed while he was motoring along 30 miles offshore and the boat filled up with water and sank, that’s a potentially horrific safety issue in my view. But, I can tell you that in my time sitting in on electrical committee meetings with the ABYC, I’ve never heard this issue brought up.
Finally here, to Ken’s mention of megohm tests for boats. Again, for those of you not familiar with such testing, this type of test is used to test the integrity of electrical insulation and involves shooting a pretty high voltage through the system and determining if there are any breakdowns in electrical resistance or insulation that could cause a problem. In commercial boating environments, this procedure is actually a requirement as part of periodic inspections. It is really quite an involved procedure to perform a comprehensive megohm test on a modern boat’s electrical system. Statistically, I can tell you that the number of system failures like the one described in “To Bond or Not to Bond” is so small, that in spite of the severity of that situation, the number of actual incidents like it in a given year are so small, I could never sell the concept of a required megohm test or cathodic protection level test to the committee that governs these things. Plain and simply, there is not enough of a demonstrated needs for such tests.