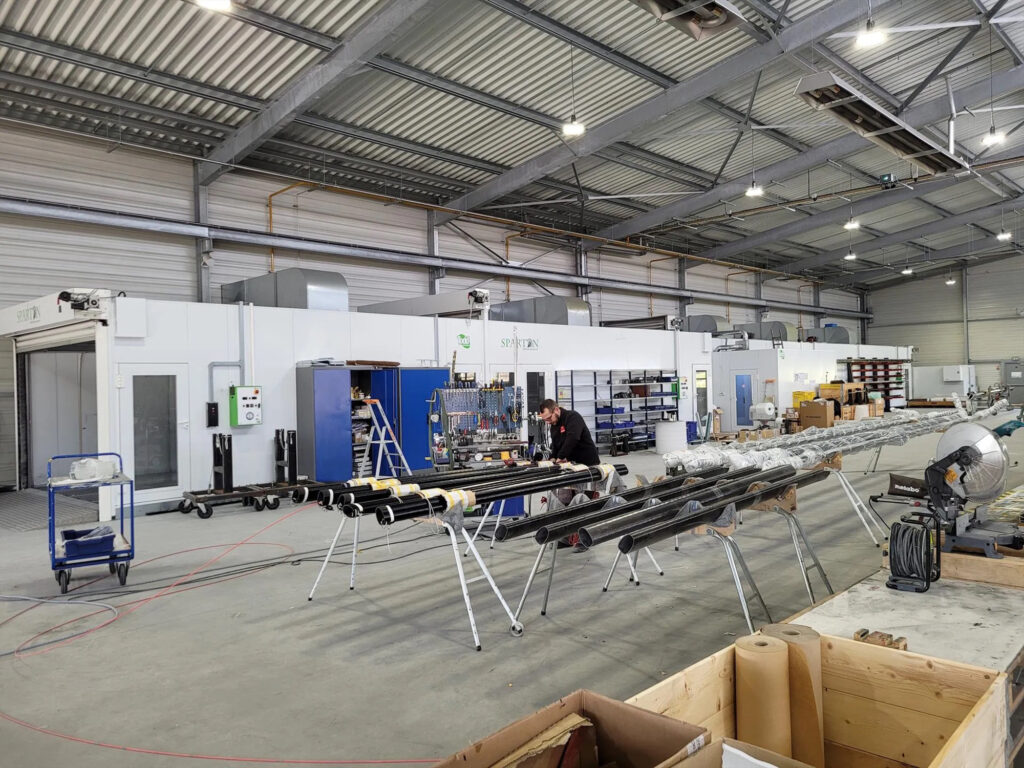
Seldén Mast recently held the official inauguration for a carbon-fiber facility in France.
Since 2002, all production of carbon-fiber masts, booms, spinnaker poles and bowsprits has been concentrated at Seldén Mast Ltd. in the United Kingdom. To meet increasing demand, the Seldén Group says, it is supplementing its manufacturing capacity with an additional production unit.
“Our product mix has been expanded in recent years with carbon-fiber furling masts, and we are pleased that the demand for these masts is high,” Seldén Group CEO Peter Rönnbäck stated in a press release. “They take a relatively long time to complete, so in order to be able to take advantage of the opportunities we have with old and new customers, we have expanded our factory in France with a hall for winding, hardening, processing and painting carbon-fiber masts. This facility will complement our factory in England.”
Seldén Mast SAS in Le Poiré-sur-Vie, France, is a 35,500-square-foot facility that Seldén built in 2007. It has been the hub for the distribution of stock items and the production of aluminum masts for customers in France and southern Europe.
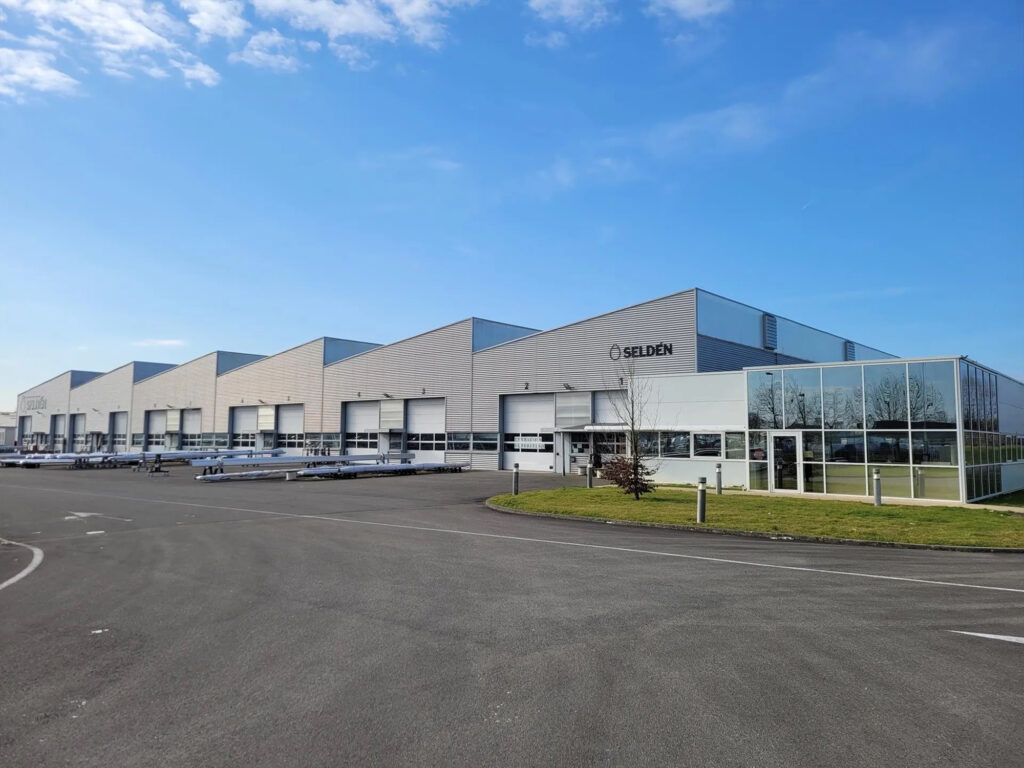
The new carbon-fiber production hall is an extension of another 19,400 square feet. According to Seldén, production has already started on masts and booms for J/70 boats, among other one-offs and OEM masts.
What is the production method that Seldén uses? It’s called mandrel filament winding. A long, aluminum mandrel rotates under CNC-controlled application of pre-impregnated carbon-fiber tows. After winding, the laminate is cured and compressed with heat and pressure in an autoclave. The mandrel is then separated from the laminate, resulting in a tube that is processed and painted in a spray booth.
Where to learn more: visit seldenmast.com