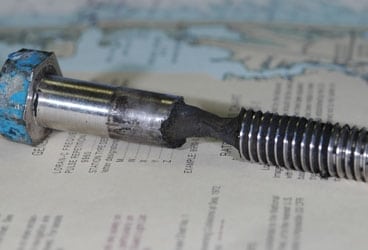
stainless corrosion 368
It comes as a surprise to many that the primary alloy contained within stainless steel is humble and familiar iron. But there’s a reason, after all, that this manufactured metal is called stainless steel. To this mundane and plentiful iron ore other, more exotic, alloys-such as chromium and nickel-are added, giving stainless steel its corrosion-resistant properties. The chromium enables stainless steel to form a tough oxide film as soon as, and for as long as, it’s exposed to oxygen, even while submerged, provided that the water contains oxygen; nickel increases its resistance to acid. Depending upon the role it’s called upon to fill-architectural trim, cutlery, or bow rail, for instance-differing amounts of elements are added, along with trace amounts of still more exotic materials, such as columbium and tantalum.
Essentially, there are three sub-groups of stainless steel: martensitic, which is often used for cutlery, many fasteners, and turbine blades; ferritic, which is used for automotive trim applications; and austenitic, which is used in the marine environment. Of the three, high nickel content (6 percent or more) is exclusive to the austenitic or marine grade. Thus, contrary to its silvery appearance, not all stainless steel is created equal.
Marine-grade stainless steel is further distilled into two popular alloys, both in the 300 series as designated by the American Iron and Steel Institute. For marine applications, the most common of these are 304 and 316. The alloy ratio used in 304 stainless steel consists of 18 percent to 20 percent of chromium and 8 percent to 12 percent of nickel, which are added to conventional carbon steel. For this reason, 304 stainless steel is often referred to as 18-8. The alloy ratios for 316 stainless steel, on the other hand, are 16 percent to 18 percent of chromium and 8 percent to 12 percent of nickel, as well as 2 percent to 3 percent of molybdenum. The final ingredient aids 316’s ability to resist a phenomenon referred to as crevice or pitting corrosion. Indeed, crevice corrosion is one of the few chinks in stainless steel’s armor.
By far, the most common variety of “marine grade” stainless steel is 304, or 18-8. As one might expect, this is a function of expense; because of the alloying-element content, 304 is cheaper to manufacture than 316. Nearly all commonly available stainless-steel fasteners, from the smallest tapping screw to large nuts and bolts, are manufactured from 304 alloys. Fasteners, machine screws, and nuts and bolts manufactured from 316 alloy stainless steel are available, but they must nearly always be special ordered, which, once again, is a reflection of their cost.
Stainless steel’s primary weakness, the aforementioned crevice or pitting corrosion (there’s a scientific distinction between the two, but for the purposes of this discussion, it’s not relevant) occurs when it’s used in an oxygen-depleted environment. The tough, nearly impenetrable oxide film that forms as soon as stainless steel is exposed to air only remains intact as long as the metal is exposed to oxygen. If stainless steel is placed in an environment where it’s starved of oxygen and exposed to water, either fresh or salt, it becomes susceptible to crevice corrosion, which typically manifests itself as roughness, valleys, pitting, or even wormlike holes.
The insidiousness of crevice corrosion is that it nearly always occurs in places where it can’t be readily observed. Where stainless steel use is concerned, therefore, the bottom line is to avoid placing it in an environment where it’s exposed to stagnant, oxygen-depleted water. This “environment” most commonly occurs under a spreader or other rigging chafe gear and where fasteners penetrate hulls: on a strut, a rudder, lower dolphin-striker jaws, and strainer installations, to name a few instances. For these installations, bronze is better suited.
Steve D’Antonio contributes regularly to CW and offers services for owners, boatbuilders, and others in the marine industry through Steve D’Antonio Marine Consulting (www.stevedmarineconsulting.com).