
Since the arrival of GPS, I haven’t had much use for the chart table on my brigantine schooner, Britannia. Most of our passagemaking navigation is done on the Raymarine multifunction display on the helm pod, then transferred to a paper chart on the saloon table roughly every hour. The chart table was only used to store things that didn’t have a permanent home and as a desk for my laptop.
Considering that the chart table and seat took up over forty percent of the length of the portside saloon, it was not a very efficient utilization of space. The layout also left a lot to be desired. The space between the table and companionway ladder was a narrow 10 inches, and squeezing into the seat frequently resulted in accidentally tripping breakers on the master power distribution panel at the side of the table. The half bulkhead also impeded sliding in and out of the seats when the saloon table was up. It had to go.
Repurposing: I’ve always thought “outside the box” when contemplating new refit projects. In this instance, I found the perfect solution to my new nav area at an Orlando antique mall.
I’m a traditionalist; I wouldn’t have built a square-rigged schooner if I wasn’t. However, advancements in equipment, particularly electrical and navigational devices, should cause us to rethink some of the more traditional methods and layouts … such as chart tables. Our trusty sextant served us well on past ocean passages but now hangs in its teak box on the bulkhead, a nod towards bygone days.
I thought about extending the saloon seating into the corner, where it would have made a lovely, snug spot in a seaway. However, not having a chart table at all might be a drawback if I eventually decide to sell.
I found a compromise in one of the antique malls around Orlando, Florida, where I live. It was a beautiful secretary desk, with a hinged drop-down lid with drawers and compartments inside and four large drawers below, adding nicely to our storage. With the lid open, it is nearly the same size as the chart table and easily fit in the existing space. Unfortunately, it was stained a horrible brown/black color and I wasn’t quite sure what type of wood it was made of, but I took a chance and bought it for $214.

The Dismantling
The chart table and seat were built 9 inches higher than the remainder of the saloon sole, for which I could only think of one reason: so anyone sitting there could look out the ports. I knew dismantling it would be a tough job, because in some places the molding was a sandwich of ¾-inch marine plywood plus two layers of fiberglass, all heavily bonded to the side of the hull. I christened it “Stonehenge” because the manufacturers clearly never meant it to be removed or to fall over! It certainly was well-made, but a pity it was so big and unergonomic. I think the Druids who built Stonehenge could have actually designed it better.
Before starting to dismantle this edifice, everything loose was removed from the saloon and galley, and things which could not be moved covered with cloths. I knew what was about to happen.
Unscrewing the teak chart table was easy enough, it was just sitting on top of the molding. However, it was so heavy two people had to lift it off the boat. The circuit-breaker panel at the side of the table also came out, along with the two small drawers, the cupboard and all the teak fiddles.
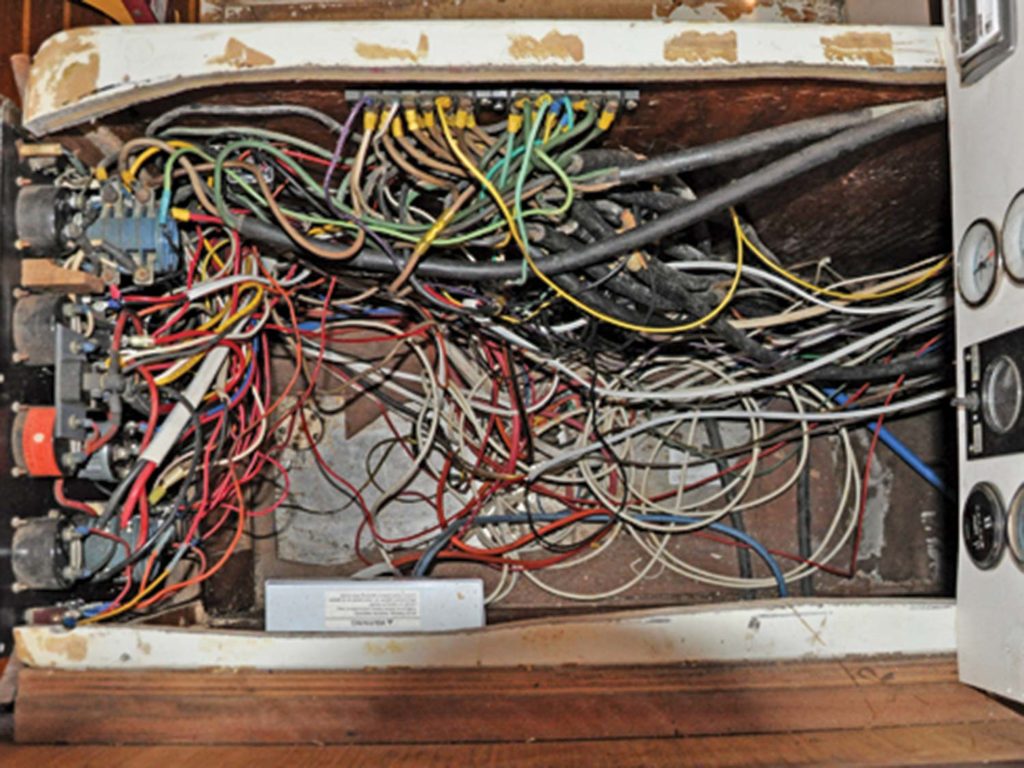
I then set about sawing the fiberglass support structure into small enough pieces to pass through the companionway. I used a combination of circular saw, reciprocating saw and oscillating cutter, along with a big hammer and pry bar! It was hard going, with fiberglass dust all over the place. I tried to minimize this by positioning my Shop-Vac nozzle near the cutting edges of the saws. Altogether, including the chart table, the pieces weighed an astounding 200 pounds.
Next, I attacked the half bulkhead which no longer needed to be so high. This was two sections of ¾-inch plywood bulkheads, with fiberglass in between. I cut the inner bulkhead out, carefully removed the teak edging trim, reshaped the panels and then refitted the trim to form an arm rest. During this exercise, I needed to keep the boat’s electrics running — particularly the air conditioning — so I had to be very careful not to cut through any wires.
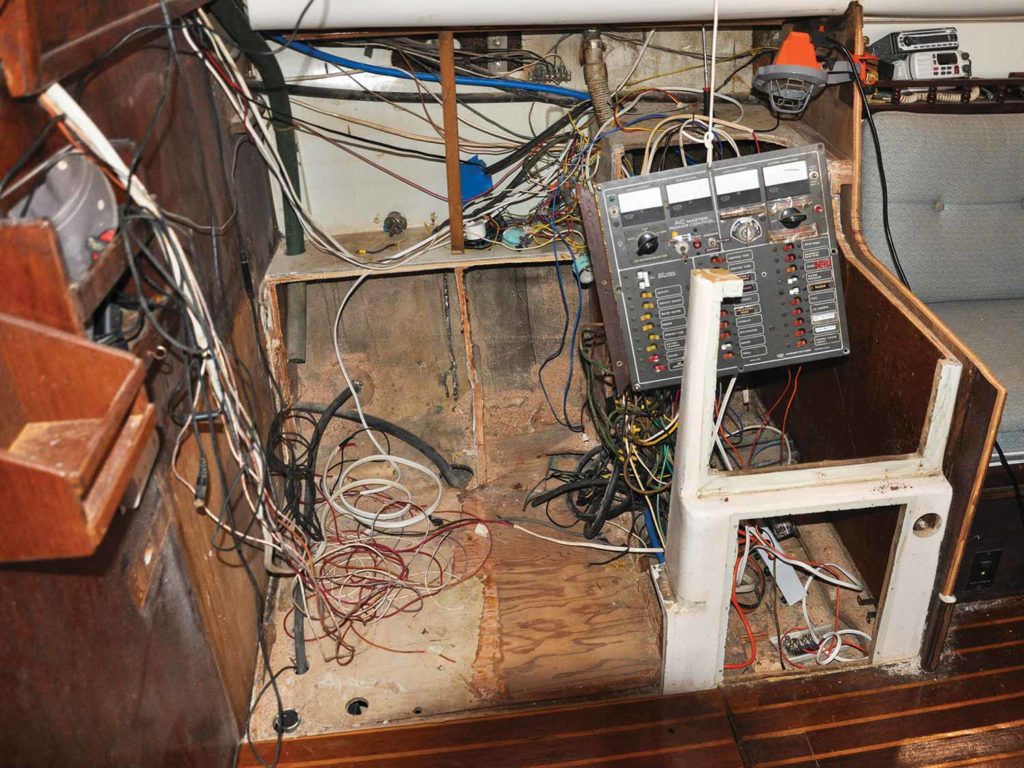
I soaked my aching back in Britannia‘s hot tub every evening.
Unfortunately, the builders had not extended the teak and holly cabin sole under the chart table, as they had on other parts of the boat. It was just raw plywood, under which were the conglomeration of wires leading to the electrical panel. I cut the floor completely out and after rerouting the wires I made a new floor with ¾-inch plywood, including a hatch to give easy access to three seacocks and filters below.
With Stonehenge fully excavated, I now had a large open space to play with.
Wired Up: For the new wiring, a 20-foot length of multi conductor cable solved the problem of purchasing individual lengths of wires and saved a bundle in the process.
The Rewiring
The next task was to relocate the electrical panel which was a spaghetti maze of wires, bus bars, connectors and relays; some were original (circa 1977), some I’d installed when I fitted new equipment. The whole conglomeration could only be described as a wiring nightmare that had needed sorting out for a long time. Some wires went to devices not in the cockpit and some to the engine instruments mounted lower down on the pedestal.
Rewiring the panel, with its hodgepodge of wires, could easily turn into a real mess if I got the wires muddled up. At moments like this, my wife always reminds me of the timeless sailor’s adage: “If it ain’t broke, it will be when I fix it.” Actually, that slogan really needs to be tattooed on my right arm, so I can contemplate it before I start complicated projects like this.
I planned to reposition the panel higher up, where the breakers could no longer be accidentally tripped. For this I built a teak framework under the curve of the deck, then modified a spare louvered door to give access to the wires leading to the panel above. I fitted a piece of ½-inch plywood below the panel to carry the four generator and water-tank gauges.
There are different ways to rewire an old boat. You can buy individual lengths of wire. Or you can convert to a National Marine Electronics Association (NMEA) networking system, which interconnects nearly everything and which can be read on a multifunction display screen, including engine instruments. You can even convert to Wi-Fi wireless and have hardly any wires at all. The last two options were well outside my budget for this project.
I decided to use regular wire, but instead of buying individual lengths I bought a 20-foot length of multiconductor cable containing 20 wires of 14 AWG (American wire gauge). These are all different colors and very much cheaper than buying individual wires.
However, a problem can occur when using multiconductor covered wire: individual wires can become hot, even with just 12 volts. So the first thing I did, using a box cutter, was to completely strip off the outer rubber casing and pull the wire loom out. This separated the wires and made them less susceptible to overheating. I could also easily pull a few strands out of the cluster, which went to places other than the electrical master panel.

I drilled a hole in the cockpit sole and wound the cluster of wires all the way to the back of the electrical panel, supporting them as necessary. I enclosed all the wires coming out of the pod in a nice, plastic, split-wire casing, just to keep them tidy down the side of the pedestal.
I then disconnected the AC shore input and hung the distribution panel from a hook in the ceiling beams so I could easily work on the back. For temporary lighting and power, I used an extension cord direct from the marina dock.
As each wire was replaced, I switched the power back on to check if the equipment still worked. It was a slow, tedious and at times strenuous process to reach behind the panels and pull the old wires out. I also used an awful lot of crimp connectors.

On the 120-volt AC side, the heavy-duty cables leading from the two ship/shore power plugs were long enough to reach the repositioned panel and thankfully did not need extending, just sorting out from the hopeless tangle in which they had been installed.
It took four weeks to completely rewire the panel and then fix it to the framework I had built, next to where the new desk was to fit.
I was actually quite amazed that everything continued to work as it had previously. For once I proved the old adage wrong. I didn’t actually need that tattoo just to remember to work carefully and methodically.
Think Boldly: One thing I’ve learned in my many projects is that space can often be made more efficient, especially on small boats, than the original layouts. It just takes a little courage!
The Nice New Desk
During breaks between all this dismantling and rewiring, I found time to renovate the bureau/desk in my garage. The moment I put my sander to it I knew I had a gem; it was real wood with a beautiful walnut veneer! It was therefore a pleasure to strip all the stain, clean the veneer and revarnish it with Total Boat wood varnish from Jamestown Distributors. I even found some ornate brass drawer handles online to replace the horrible black-painted handles. They were only $2 each and look superb on the curved walnut drawers.
To fit my large-screen laptop, I removed the vertical dividers and mounted the five small drawers in the top of the desk. With the flap open, the table is about the same size as the original nav table, but when closed it takes up less than half the space.
I hoped my companionway measurements were accurate as my wife and I carefully manhandled the posh new desk down the deck and into the cockpit, trying not to scratch the newly varnished sides. On its side, it slid through the opening with about a half inch to spare. Whew. But an inch is as good as a fathom for a job like this. The desk then slid sideways and fit under the curve of the deck. I infilled between the ornate feet with a plywood plinth to stop things from rolling under the desk.
I already had a comfortable folding deck chair which nestled perfectly up to the desk, and it can be used at the dining table when needed. As an added touch, I bought an antique-looking globe for bottle storage that fits nicely next to the bureau. This is located in two teak collars in the floor. It is now considerably easier and much more comfortable to sit at the desk, and the saloon appears very much bigger. The electrical panel is easier to operate, and not a single breaker has been accidentally tripped. I even sold the old chart table, offsetting some of the cost.
The remodeled area is now more akin to a neat little office than a boat’s navigation area. Smaller boats than Britannia might greatly increase living space by redesigning their chart table area. It just needs a bit of bold thinking.
Serial do-it-yourselfer Roger Hughes is a frequent contributor to Cruising World.
Materials, Costs & Suppliers
Sheet of plywood
Local hardware store $47
Multiconductor wire
wireandcableyourway.com $75
Terminal connectors
Local hardware store $20
Secretary desk
Local antique mall $214
Varnish for desk
jamestowndistributors.com $32
New drawer handles
lawlesshardware.com $23
Bar globe
homedepot.com $96
Sale of chart table ($100)
Total $407